Remaining Charge and 100% Capacity
How well does your BMS determine current capacity?
Users of devices with batteries find it very important to have a good indication of how long the battery in their device will last.
Without a good capacity indication, the device may shut down and the battery needs to be recharged first.
For vehicles, that can make the difference between getting home or not. Or reaching a charging station, or not.
The importance
Every battery will sooner or later run out of power and energy. This is not to say that this is always a problem. With a flashlight, no one finds it strange that the light fades and eventually goes out. With a shaver, it is already annoying if it only just shaves half of your face. And for a car, it is extremely inconvenient when you are stranded with an empty battery 10km from the next charging station.
Is it really so difficult to find out how much energy is left in a battery?
Complex
There are many factors that influence the remaining charge of a battery. Most batteries perform badly at low temperatures (especially below freezing). Then the capacity decreases drastically. But also the usage time of a battery will decrease the 100% capacity. In addition, there may be a bad or damaged cell in use, whose capacity decreases faster than the others.
Manufacturers are therefore reluctant to use a clear State-of-Charge (SoC) indication on their batteries and products.
After all, what a customer does not know cannot lead to complaints.
However, for many users a good SoC indication is extremely important. For them, it saves working time of their tools.
They assume (usually wrongly) that the operating time indication is ‘magically’ correct.
Battery suppliers prefer not to burn their fingers on a hard specification and often just let their customers choose which BMS they want.
Some have no indication, others e.g. only 4 or 5 Leds. A nice rough indication.
Then they, as a battery manufacturer, are not responsible for its quality and when the SoC indication is unreliable.
But who should have the most knowledge about the BMS and the SoC determination? The battery supplier or his customer?
A customer of an autonomous robot for warehouses used a Lithium battery from a large German company.
After a few months, many of the devices were only able to run for a short time and had to be recharged more often. Upon inspection it appeared that the BMS thought the battery was empty, while in reality it was still 50% full.
The opposite also occurred: the BMS thought there was still enough charge, but the device stopped, thus blocking passage for others.
This caused the warehouse work to come to a complete standstill.
Self Learning
The SoC (State-of-Charge) gives the percentage of capacity relative to 100% charge. But to know how far you can go, an absolute number of the available capacity is needed. This can be expressed in Ah (Amp-Hour) or Wh (Watt-Hour). Then the BMS also needs to know the 100% capacity in addition to the SoC, and adjust it when cells age.
The Magic
The BMS can determine the remaining capacity in several ways.
- Based on current over time integration.
By keeping track of how much current goes into or out of the battery, the Amp-Hour number is determined. - Based on voltage.
Here the voltage is used to look up the remaining charge (State-of-Charge) in a table. - Based on a combination of voltage and current.
With this combination, the advantages of the previous methods can be used to compensate for the disadvantages of the other method.
Current Measurement
The most common method of determining the SoC is by measuring the current and integrating the amount of current over time.
Because it is actually about charge, and the unit of charge is ‘Coulomb’, this method is called Coulomb-counting.
One problem with this method is that changes that cannot be seen in the current measurement (self-discharge, aging, and drift) cannot actually
be accounted for, so the SoC starts to deviate more and more from the actual remaining charge.
Therefore, the SoC needs to be adjusted under certain conditions, e.g. after (full) charging.
But, when that condition is never met in the used application, the deviations still occur.
Voltage measurement
In the voltage-SoC method, the voltage of the battery is measured and the SoC value is looked up in a table. The table must be determined per cell type, because differences in cells lead to deviations. With a good table the correct relative residual charge is always displayed, even with self-discharge and aging. But it is relative, as a percentage of 100%, while the user needs the absolute residual value.
This relative value is only correct when the battery is at rest.
A load current will cause the voltage to drop, resulting in a false indication.
So here too there is a condition. If in the application the battery never (or rarely) comes to rest, the capacity determination is incorrect.
But by using a model of the cell, the voltage under load can be corrected so that the table can still be used.
Then the model of the cell must be determined, and programmed into the BMS.
Current-voltage combination
It is therefore obvious to combine the Coulomb-counting with the voltage-SoC method so that self-discharge, aging, drift
or inferior cells, have no influence anymore and the absolute remaining charge is known and accurate.
The algorithm calculates both the SoC and SoH (State of Health), so you can also see when a battery needs replacing.
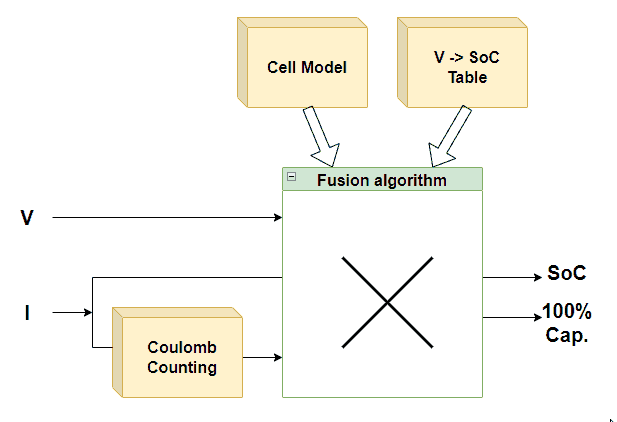
Fusion algorithm for State of Charge
Engineering Spirit’s BMSs (and its trademark Axtrel.com
) are therefore
equipped with a unique algorithm that processes the current and voltage measurement per cell into a SoC reading and absolute remaining capacity.
For optimal results, the voltage SoC table and cell model are determined at different temperatures.
When for an application, the SoC less accurate is allowed, we work with standard values.
A telephone conversation with our technologist will quickly tell you.